How do we work
1.Drawing Analysis
Upon receiving the 3D file, we will conduct a comprehensive 3D file analysis, including Wall Thickness analysis, Draft Angle analysis, Undercut Analysis. This process ensures early optimization to avoid mold modifications or scrapping in later stages. Additionally, our engineering team can assist with optimizing drawings and obtaining confirmations, saving valuable time.
1)Wall Thickness Analysis
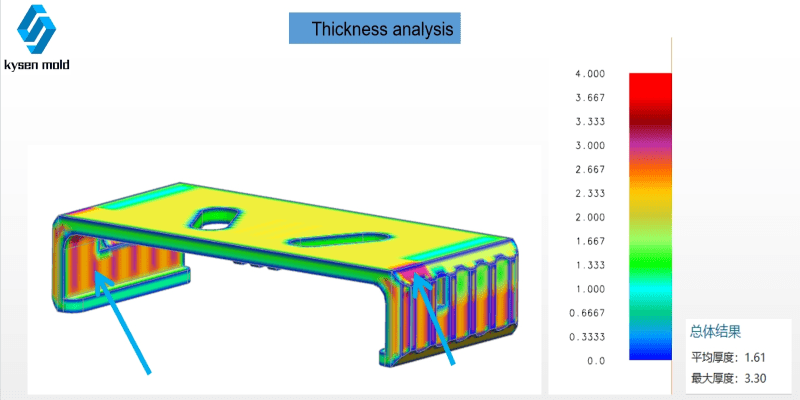 |
1.If the wall thickness is too thick, shrinkage may occur during injection molding. We will analyze this issue in advance and optimize it to an appropriate thickness based on the product structure, thereby mitigating mold investment risks.
2.According to the thickness analysis, The average thickness is around 1.61mm, the thickness marked with red area is about 3.3mm,there will have sinkmark for the uneven thickness.
3.We suggest to reduce the the thickness to be 2mm to optimize file.
|
2)Draft Angle Analysis
Products without a draft angle may be scratched during injection molding production, resulting in surface imperfections that affect product quality. We recommend suitable draft angles according to the product structure to prevent such issues.
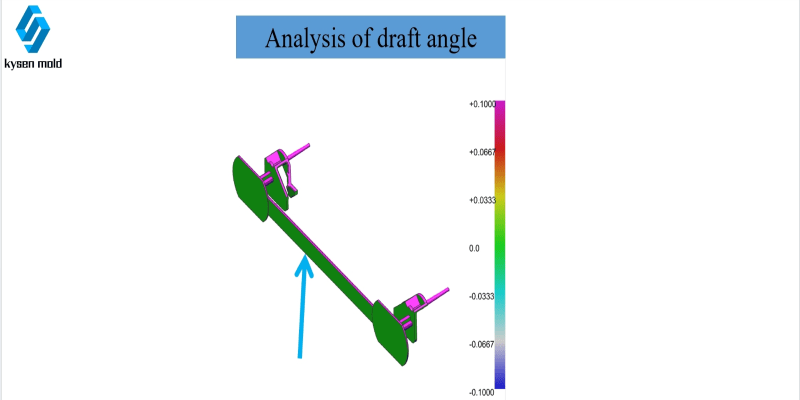 |
Problem: Based on the analysis of draft, the green side indicated by the arrow lacks a Draft Angle.
Result: The absence of a Draft Angle may cause the product to be scratcheden the product take off from mold.
Our advice: We recommend increasing the Draft Angle by 0.5° to avoid the risk of mold-related scratching. If necessary, we can assist in further improvements.
|
3)Undercut Analysis
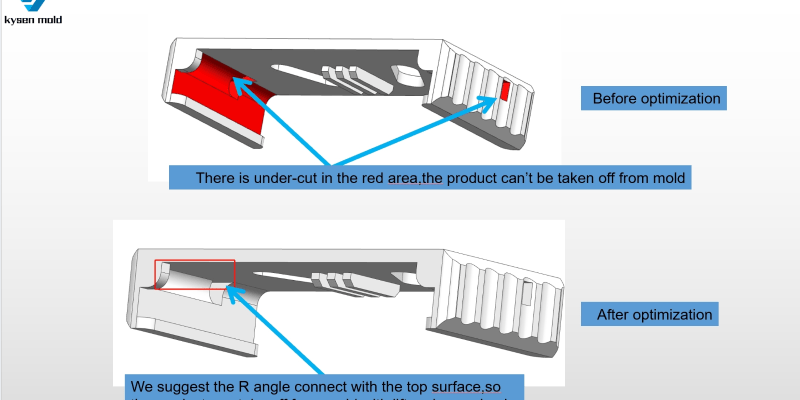 |
Undercut designs that cannot be realized in molds are a common issue in product design. While it may appear feasible in 3D drawings, they often cannot be manufactured in molds. Therefore, feedback and optimization must occur before mold creation to avoid subsequent mold modification or scrapping risks. Our engineers will assist with optimizing drawings and sending them for confirmation. |
4)Cost Saving
For products intended for market testing with small quantities, we typically make replaceable mold cavities for you , reducing mold costs by approximately 50%. If additional cost-saving solutions are identified, we will provide recommendations for your consideration.
2.Design of 3D Drawings
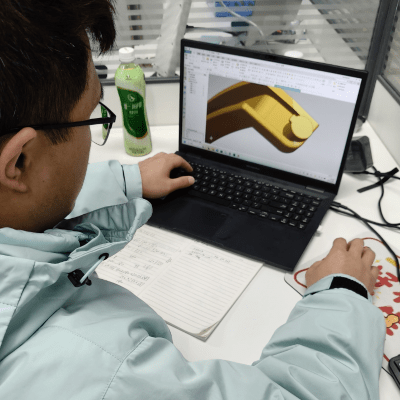 |
If no 3D file is available, do not worry. Communicate your ideas with our salesman, and our engineers will design 3D drawings based on your concepts or samples. These drawings will then be sent to you for review and confirmation, streamlining project progress and reducing the need for external designers. |
3.Order Confirmation
Each time we update drawings, we provide customers with feedback until the final drawings, customers confirm there is no problem before placing an order. Our sales team is available 24/7 to ensure timely and effective communication, addressing any concerns promptly and advancing the project efficiently.
4.DFM Report
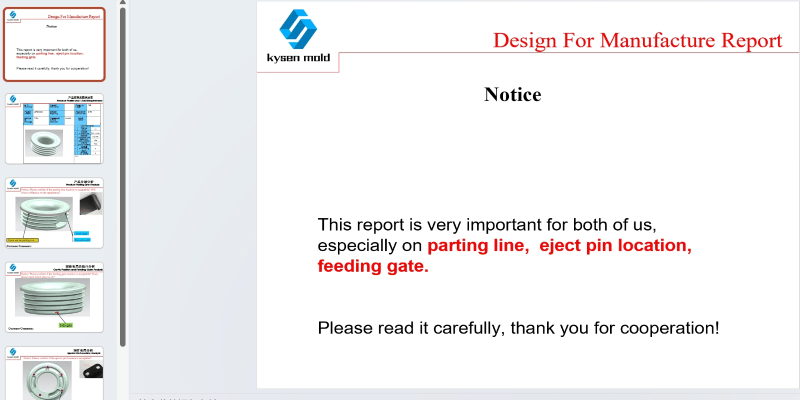 |
We will generate a DFM report based on the final 3D drawing and send it to you for review and confirmation. This report provides insights into mold manufacturing processes, including parting line locations, feeding gate types and location, eject pin location, etc., while minimizing mold investment risks. |
5.Mold Drawing Design
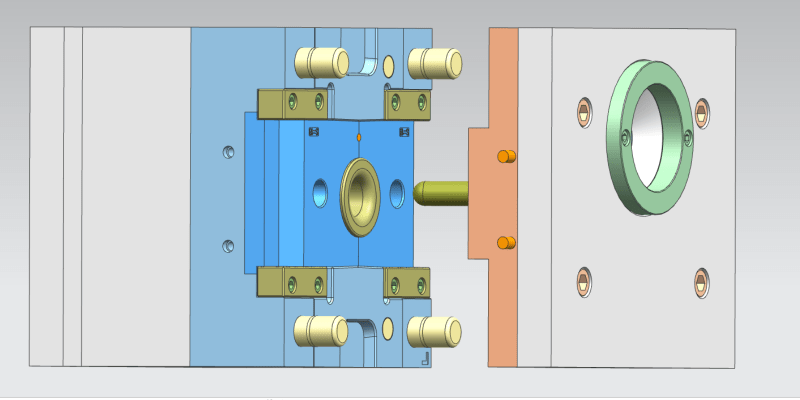 |
Our engineers will design the 3D mold drawing using their professional expertise and confirmed DFM data. Mold drawings are critical in the mold processing workflow, detailing all mold components and guiding the manufacturing process. |
6.Purchase of Mold Steels and Accessories
Once the mold drawing is approved, we will purchase mold steel and accessories as per the drawing specifications to prepare for mold processing.
7.Mold Processing
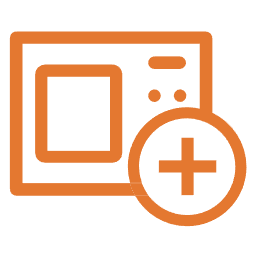 |
Milling Machines and Lathes
After receiving steels, we perform rough machining using milling machines and lathes. Subsequent steps include rough cutting precision machining, drilling, boring, fine machining, and threading.
|
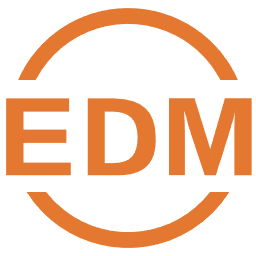 |
EDM Processing
EDM machines handle complex details, shapes, and hard materials, ensuring high-quality surface finishes.
|
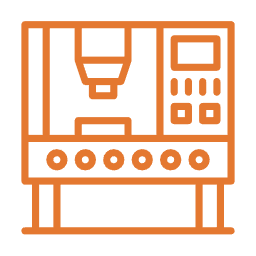 |
CNC Machining
CNC machines excel in precision cutting, drilling, milling, engraving, and tooling for complex profiles of mold parts.
|
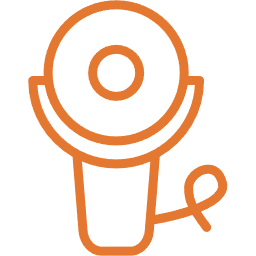 |
Grinding and Polishing
These processes achieve smooth surfaces, accurate dimensions, and enhanced mold surface quality.
|
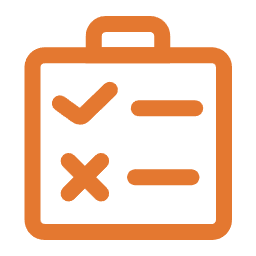 |
Assembly and Testing
During assembly and testing, we ensure precise alignment, functional verification, and accuracy of mold components before final production.
|
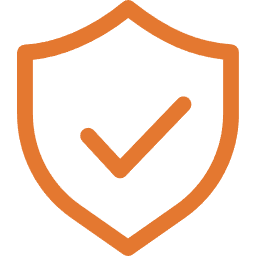 |
Quality Check
Quality checks encompass dimensional accuracy, surface finish, and functionality to ensure compliance with design specifications.
|
8.Send Mold Sample
After mold testing, we first inspect and evaluate internal samples. Any correctable issues are addressed promptly to save transportation time. Subsequently, we send the mold sample to you free of charge for physical inspection, size testing, and assembly verification. Based on your feedback, we refine the mold to prevent batch production problems.
9.Injection Mass Production
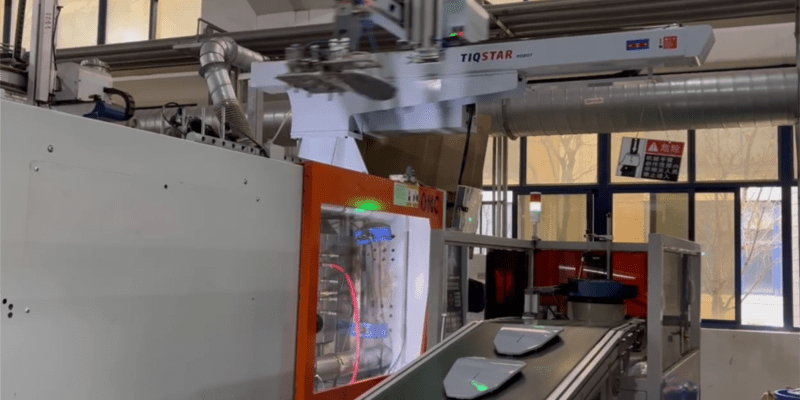 |
Upon the mold sample are approved, we prepare for mass production. Equipped with 21 injection molding machines of varying sizes and fully automatic robotic arms, we ensure high production efficiency and stable product quality. Quality control includes in-process inspections and post-production sampling inspections, avoiding issues discovered after delivery. |
10.One-Stop Service
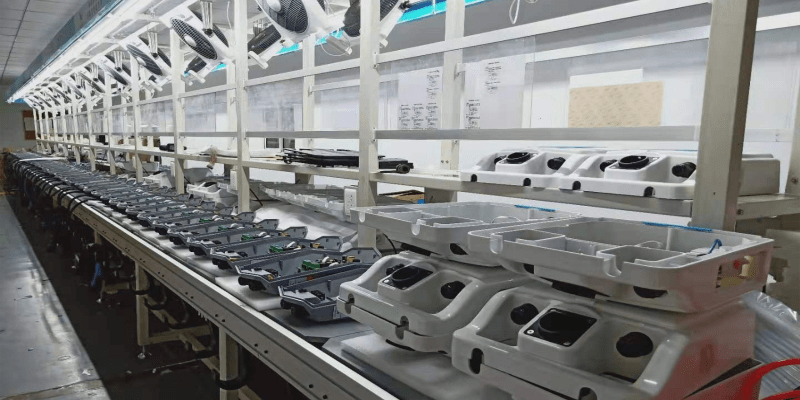 |
If the project requires printing, custom packaging, or assembly, we offer one-stop services to streamline the process and save turnaround time. |
11.Goods Delivery
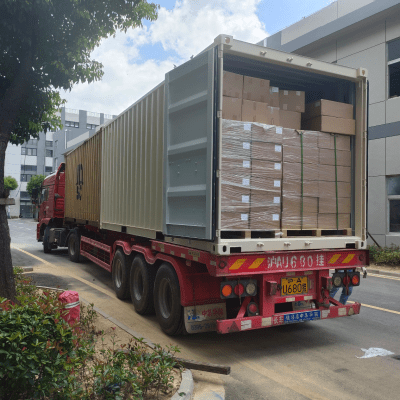 |
Our professional logistics department provides competitive channels and pricing. Based on delivery address, box count, weight, and volume, we offer suitable transportation options for your reference. Typically, we operate under DDP terms, handling tariffs, customs clearance, and other procedures so you only need to wait for delivery at home and don’t need to pay for any tax cost etc. |